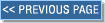 |
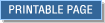 |
 |
TEXTURED HDPE GEOMEMBRANE
METRIC UNITS
|
|
Minimum Average
Values |
Property |
Test Method |
1.00 mm |
1.50 mm |
2.00 mm |
2.50 mm |
|
Thickness, microns |
ASTM D 5994 |
|
|
|
|
minimum average |
|
950 |
1,425 |
1,900 |
2,375 |
lowest individual of 8 of 10 readings |
900 |
1,350 |
1,800 |
2,250 |
lowest individual of 10 readings |
850 |
1,275 |
1,700 |
2,125 |
|
Asperity Height, microns |
ASTM D 7466 |
250 |
250 |
250 |
250 |
|
Sheet Density, g/cc |
ASTM D 1505/D 792 |
0.940 |
0.940 |
0.940 |
0.940 |
|
Tensile Properties
1 |
ASTM D 6993
|
|
|
|
|
1. Yield Strength, kN/m |
|
15 |
22 |
29 |
37 |
2. Break Strength, kN/m |
|
11 |
16 |
21 |
26 |
3. Yield Elongation, % |
|
12 |
12 |
12 |
12 |
4. Break Elongation, % |
|
100 |
100 |
100 |
100 |
|
Tear Resistance, N |
ASTM D 1004 |
125 |
187 |
249 |
311 |
|
Puncture Resistance, N |
ASTM D 4833 |
267 |
400 |
534 |
667 |
|
Stress Crack Resistance
2, hrs |
ASTM D 5397 (App.) |
300 |
300 |
300 |
300 |
|
Carbon Black Content
3, % |
ASTM D 1603 |
2.0 - 3.0 |
2.0 - 3.0 |
2.0 - 3.0 |
2.0 - 3.0 |
|
Carbon Black Dispersion
4 |
ASTM D 5596 |
-Note 4- |
|
Oxidate Induction Time (OIT) |
|
|
|
|
|
Standard OIT, minutes |
ASTM D 3895 |
100 |
100 |
100 |
100 |
|
Oven Aging at 85°C |
ASTM D 5721 |
|
|
|
|
High Pressure OIT
(% retained after 90 days) |
ASTM D 5885 |
80 |
80 |
80 |
80 |
|
UV Resistance
5 |
ASTM D 7238 |
|
|
|
|
High Pressure OIT
6 (% retained after 1600 hrs) |
ASTM D 5885 |
50 |
50 |
50 |
50 |
|
Roll Dimensions |
|
|
|
|
|
1. Width (meters): |
|
7 |
7 |
7 |
7 |
2. Length (meters) |
|
228.7 |
152.4 |
114.3 |
91.5 |
3. Area (square meters): |
|
1,603 |
1,068 |
801 |
641 |
4. Gross Weight (kilograms, approx.) |
1,588 |
1,588 |
1,574 |
1,574 |
|
1. Machine direction (MD) and cross machine direction (XMD) average values should be on the basis of 5 test specimens each
direction. Yield elongation is calculated using a gauge length of 33 mm; Break elongation is calculated using a gauge
length of 50 mm.
2. The yield stress used to calculate the applied load for the SP-NCTL test should be the mean value via MQC testing.
3. Other methods such as ASTM D 4218 or microwave methods are acceptable if an appropriate correlation can be established.
4. Carbon black dispersion for 10 different views: 9 in Categories 1 and 2 with one allowed in category 3.
5. The condition of the test should be 20 hr. UV cycle at 75°C followed by 4 hr. condensation 60°C.
6. UV resistance is based on percent retained value regardless of the original HP-OIT value.
This data is provided for informational purposes only and is not intended as a warranty or guarantee. Poly-America assumes no responsibility in connection with the use of this data. These values are subject to change without notice. REV. 08/11
|
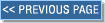 |
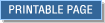 |
 |
|
 |
 |
 |
 |
 |
|